The Situation
This large manufacturing company specializing in industrial cooling towers was experiencing endurance issues with their coatings and suffering from slow turnaround times.
The cooling towers that their steel parts were used in are high humidity environments which really test the durability of the paint. They had used various coaters over the past ten years, but the paint would not hold up in the field. The manufacturer had a 5-year paint guarantee in place with lots of supporting marketing material tied to that guarantee.
PowderGALV® Challenge
Our challenge was to provide a durable coating that would withstand the harsh conditions and handling. This coating must last for at least five years to meet the standard for their five year guarantee. It must fit within their existing marketing strategy. The coating process must also be timely to ensure a quicker turnaround.
Powder Coating and Process Testing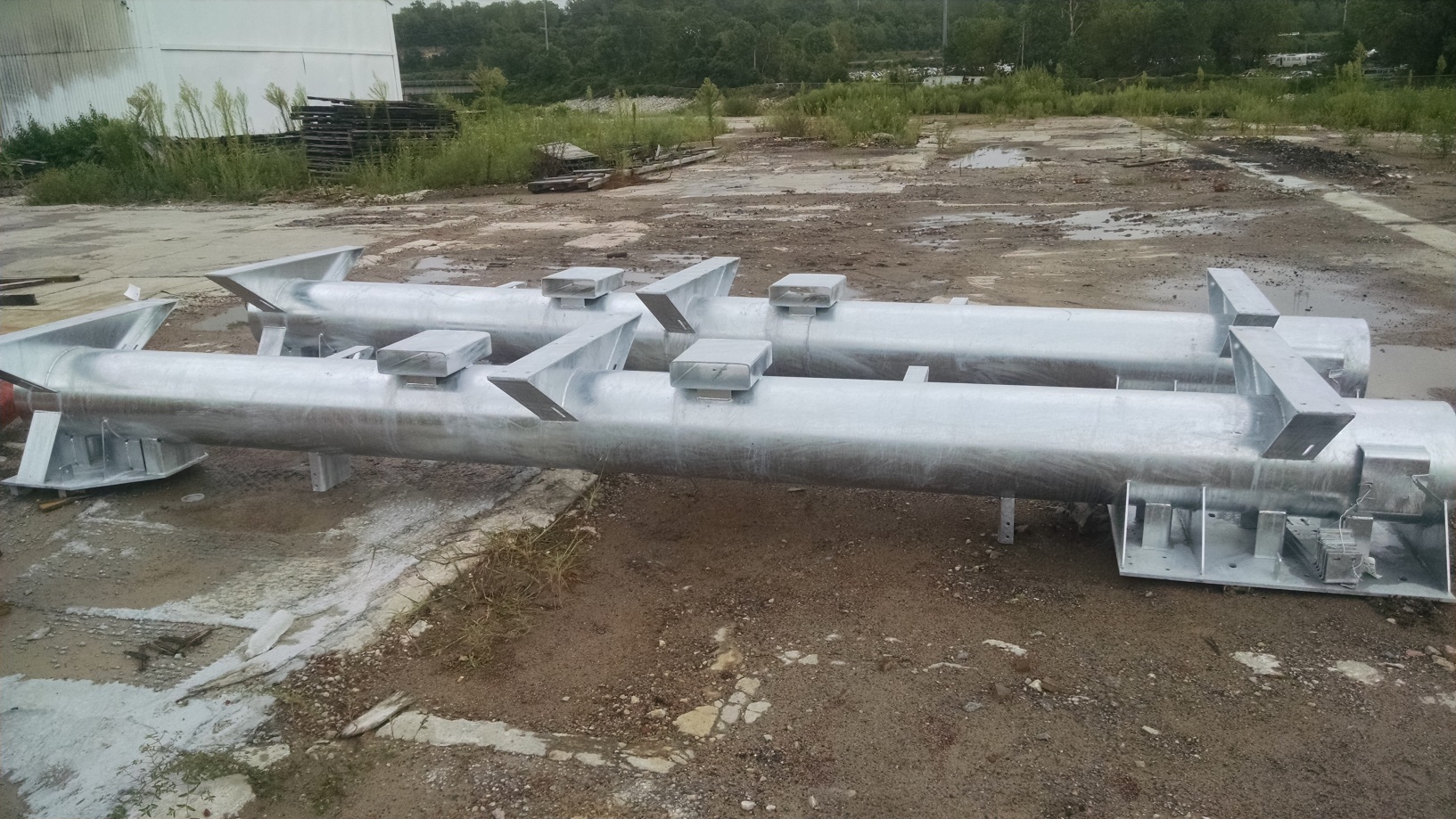
The first order of business was to provide multiple samples of various liquid coatings for comparison. We considered and tested powder coatings and used input from technical experts and suppliers. We referenced ASTM D7803-standard practice for preparation of zinc (hot-dip galvanized), coating iron and steel product, and hardware surfaces for painting. We tested and evaluated the processes and determined that the existing process was the best. Once the best coating and process was determined, we started our in-house process development.
Created New PowderGALV® Process
Our new process helped us to meet both the quality and the time restraints required by this customer. Here is a snapshot:
- Parts are hot-dip galvanized, treated, and prepped.
- The pieces are heated and dried.
- Prime coat is applied and top coated for protection, durability and color.
- Pieces are cured.
- Quality check done on all pieces.
- Order is packed out and picked up by customer.
Custom Solution
Through our customer’s testing facility, they determined this process to meet or exceed their standards placed on the liquid process. The field results are meeting their standards for handling and durability.The powder coating material and application was designed to meet the existing marketing strategy. Parts are available at 50-75% faster rate. Expedited projects are available in days instead of weeks.
Click to See How PowderGALV® Helped This Customer Predict Double the Jobs for the Upcoming Year